
MRG’s experts have been performing in-depth oil analysis for over 25 years. Our Lube Oil Analysis monitors the health of oil-lubricated equipment with a comprehensive testing slate. Oils are assessed in three categories: wear, oxidation and physical properties. While our standard oil analysis slate provides comprehensive oil health analysis, some customers require additional testing. If you require rather testing beyond the standard slate, please contact us.
STANDARD OIL ANALYSIS SLATE

RDE Spectroscopy
This atomic emission spectroscopy method quantifies the elements present in the lubricant. These elements include wear metals such as magnesium and phosphorus, copper and zinc, and grease thickeners such as calcium and sodium. This method can then be used to evaluate wear and contamination properties of a sample.
A small portion of the dissolved sample is ignited between two carbon electrodes. The wavelengths of light that are emitted by the sample as it burns are measured. These wavelengths of light and their relative intensity are used to quantify the individual elements present.
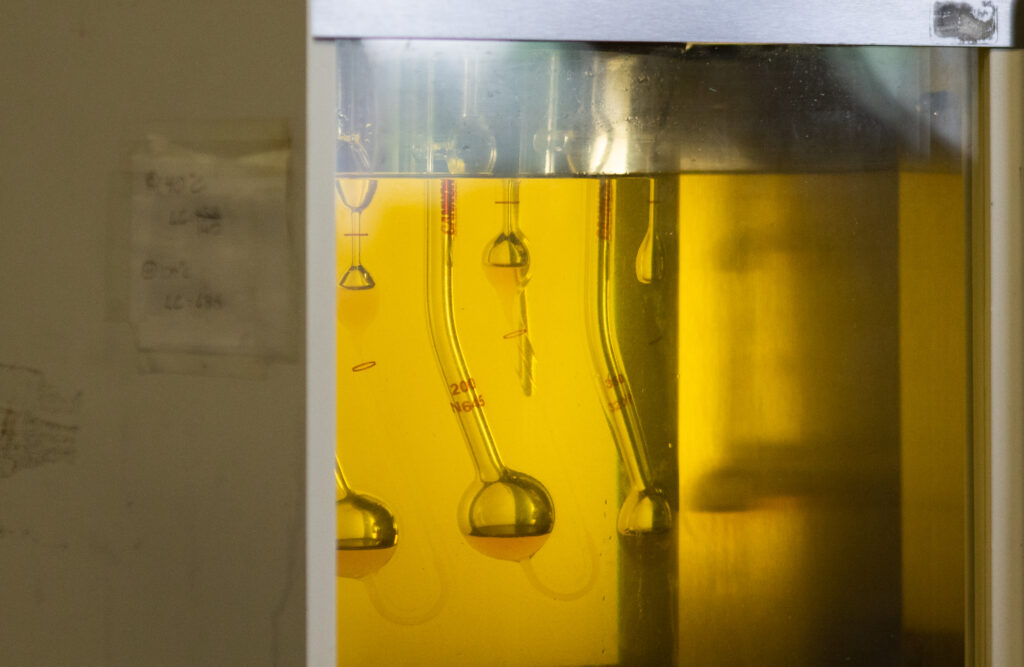
Viscosity for Oil Analysis
Kinetic Viscosity measurements ensure that the viscosity of the oil is within the normal change.
Oil is placed in a u-tube with capillary and inserted into a constant temperature bath that remains at 40 degrees Celsius. The time required for the oil to pass through the capillary is measured. The time is converted into the viscosity using the viscosity constant of the u-tube and reported centiStokes.
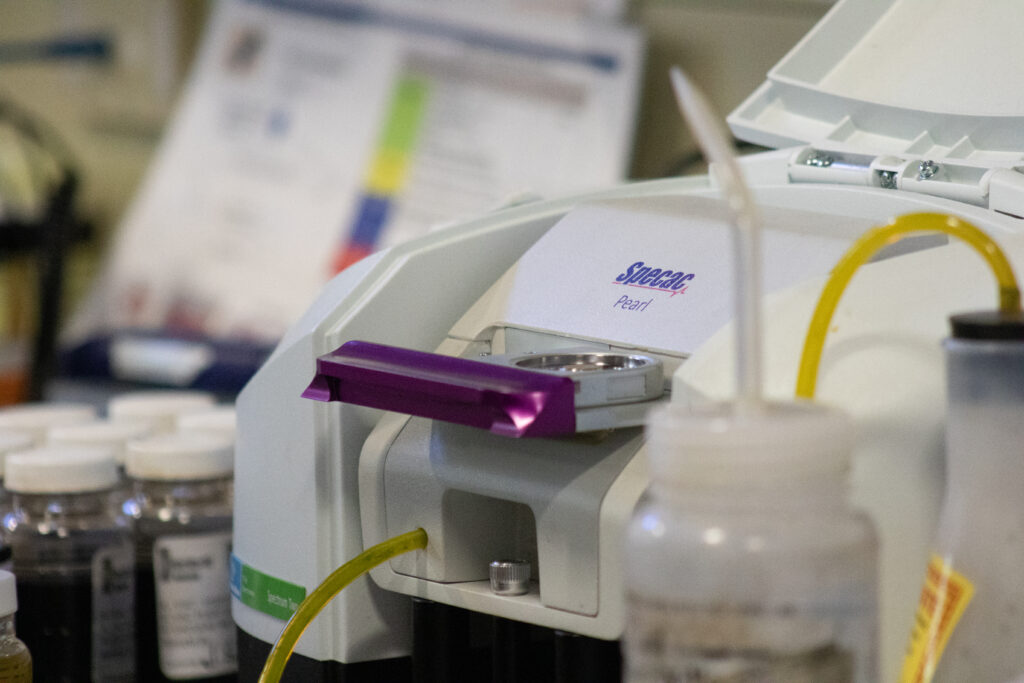
FT-IR Spectroscopy
FT-IR is used to determine the chemical properties of a compound in a qualitative manner. Oxidation products, contamination and mixing with incompatible greases are easily detected using this technique.
A small quantity of grease is subjected to a spectrum of infrared radiation. Specific wavelengths of infrared radiation excite the chemical bonds that make up the grease and generate a unique spectral fingerprint. This can then be compared to baseline data to determine chemical changes in grease composition.
R.U.L.E.R.
The percent of antioxidant additive package that remains in the lubricant is compared to the baseline. This test shows if the lubricant is at an elevated risk for oxidation.
A portion of the lubricant is exposed to a solvent that extracts antioxidants from the lubricant. This extract is subjected to linear sweep voltammeter which measures the change in current as a conducting compound and is subjected to linearly increasing potential. The current response of the sample is compared to a baseline to determine the percent of antioxidant protection that remains quantified in order to measure grease consistency.
Particle Counting for Oil Analysis
Particle Counting quantifies the particles in an oil that are larger than 4, 6 and 14 microns. These quantities are translated into the ISO rating.
Oil is pumped through an optical chamber while a light is shown on the sample. Particles are quantified by the scattering of light as it passes through the sample.
DR-III Ferrography
This process is used to determine wear levels in oil. Measurements are made at two sizes in order to determine the severity of the ferrous debris. High levels of larges particles may indicate analytical ferrography is necessary.
This optical technique separates ferrous debris from the oil by a magnetic field. As the debris is captured by the magnetic field, it interrupts a light source that is being measured by a sensor. The decrease in light transmitted through the sample corresponds to the quantity of ferrous debris present in the sample.

Filter Efficiency Oil Filter Testing
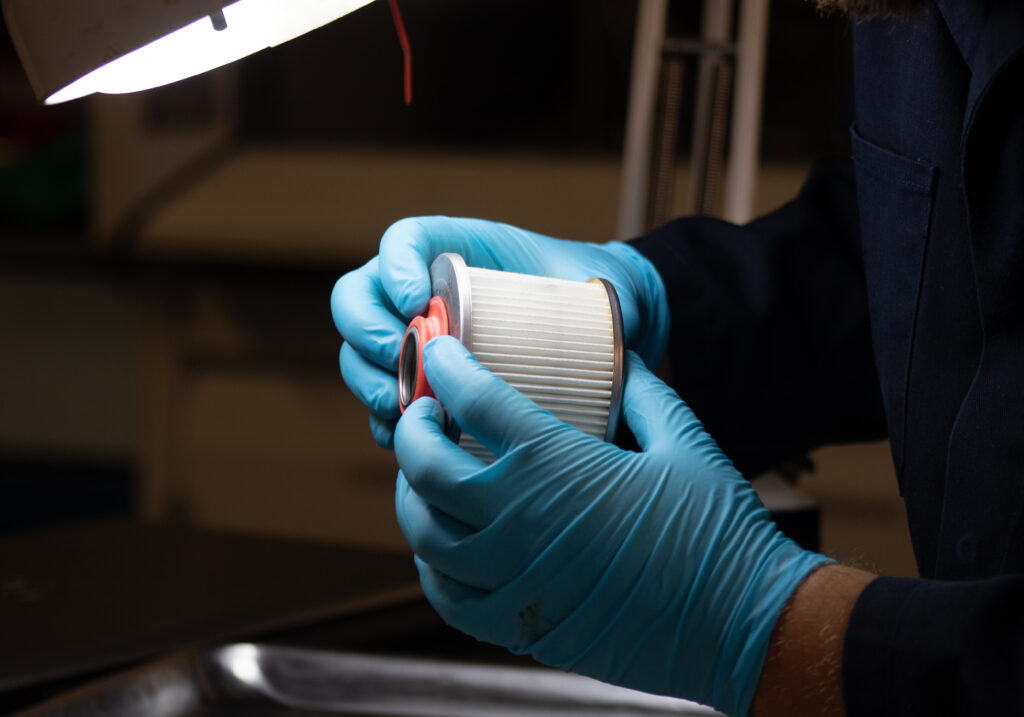
Filter Root Cause Analysis
EXTRA SERVICE OFFERINGS
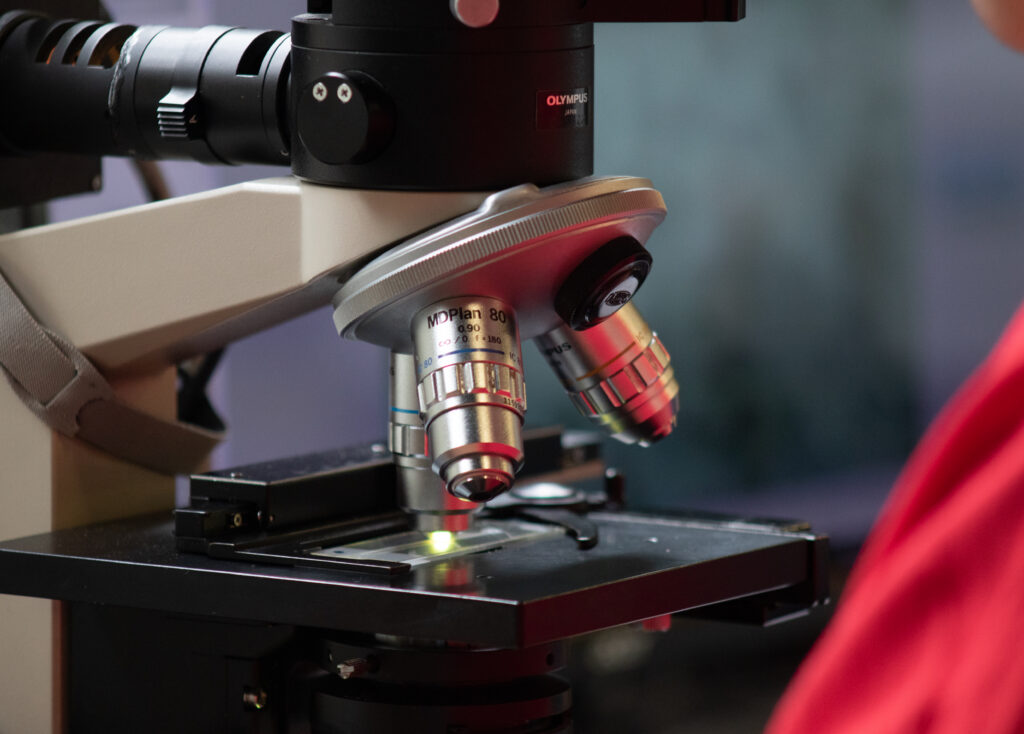
Analytical Ferrography
This process involves the examination of ferrous debris from a lubricant sample by a qualified laboratory analyst. The analyst may determine wear modes that generated wear specific particles and diagnose abnormal component conditions.
The lubricant is dissolved in an organic solvent and then slowly flows over a microscope slide that is subjected to a magnetic field. Ferrous particles are trapped on the slide while non-ferrous particles wash away. These particles are then examined under high magnification in order to assess generative wear modes.
Filter Efficiency Testing
Oil filter testing measures the efficiency of filtration using particle counting to determine before and after filter effectiveness. Actual filters may be submitted for analysis to visually inspect the filters and determine if there are problems such as rips or clogs that may be causing it to function ineffectively.
This method is done using laser-scatter particle counting methodology to determine an ISO Particle Count reported per ISO 4406. Filter inspections are performed by disassembling the filter and visually inspecting for rips or clogs in the matrix of the filter. In some cases, microscopic analysis can be done to view any problems with the filter matrix.
Membrane Patch Colorimetry (MPC)
Using method ASTM D7843, varnish potential is used to look at the amount of soft varnish particulate present in the oil. In areas of low flow or cooler conditions, soft varnish particulate can coat parts and cause seizing or sticking, ultimately leading to premature failure.
A patch is prepared per ASTM D7843 and a CIE-dE value is reported. The ranges of CIE-dE include normal, monitor, abnormal and critical.
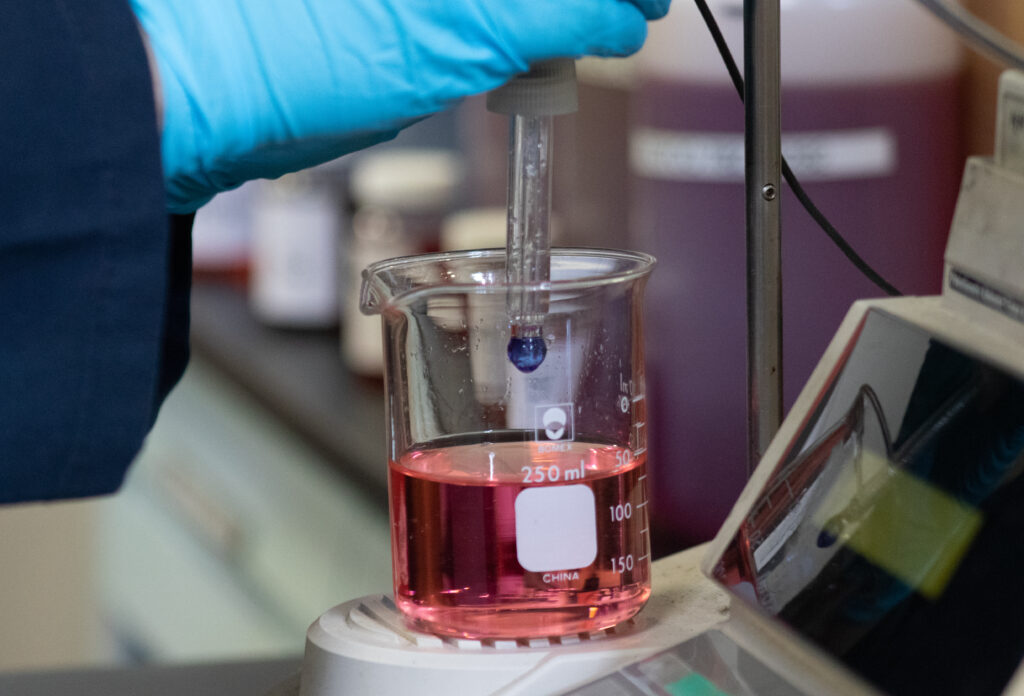
Acid Number (TAN)
Acid Number is designed to look at the total amount of acidic components present in the oil. Typically a rise in acidic concentration will result in more rapid degradation of the oil.
Acid Number is performed using a titration method. The trendable value is reported in mg KOH/g of oil.
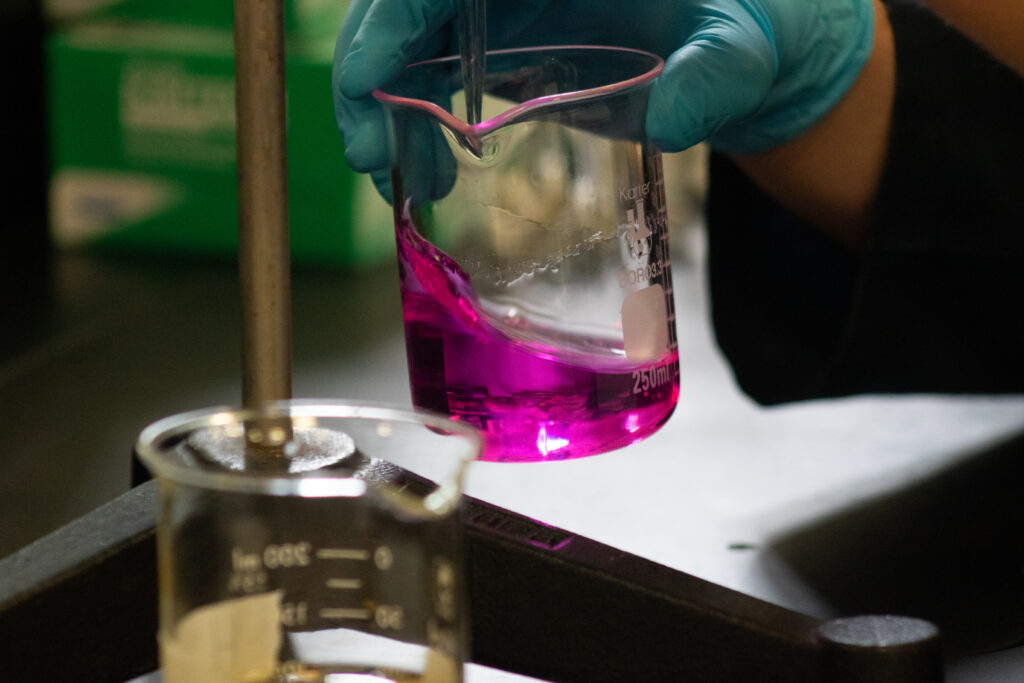
Base Number (TBN)
Base Number is designed to look at the total amount of detergent additive present in the oil. Over time the detergent additives will deplete and the base number will drop. Trending the base number value is particularly important in engine oil applications where there are blow by gases present which can quickly deplete the additive package.
Base Number is performed using a titration method. The trendable value is reported in mg KOH/g of oil.