
When a wind turbine fails, the costs can be enormous due to equipment downtime and the exceptional effort required for repair or replacement. Condition based monitoring (CBM) can greatly improve turbine reliability and reduce costs when properly applied. MRG has developed a testing method using the Grease Thief© that allows grease monitoring to become an integral part of wind turbine CBM programs.
Getting the Sampling Right
The best lab techniques in the world are useless if the samples being analyzed aren’t taken from the correct locations in the turbine. The ingenious design of Grease Thief allows for grease samples to be collected from the face of the main, yaw, pitch and generator bearings. These samples are representative of the conditions of lubricating grease and allow for truly meaningful analysis of in-service grease.The best lab techniques in the world are useless if the samples being analyzed aren’t taken from the correct locations in the turbine.
Wind Turbine Test Slate
The Wind Turbine Test Slate provides comprehensive analysis of the conditions of both the grease and the turbine. Testing for Wear, Consistency, Oxidation and Contamination describe bearing conditions without bearing disassembly. MRG has provided grease analysis for some of the largest wind energy providers in the world and detected numerous problems before they caused critical failures and costly downtime.
High Value Analysis
The MRG sampling and analysis methodology is developed from extensive testing. Sampling and analysis was performed on more than 30 different points of a main bearing to validate the recommended sampling technique. Members of the MRG team have been up tower and pulled the samples themselves.
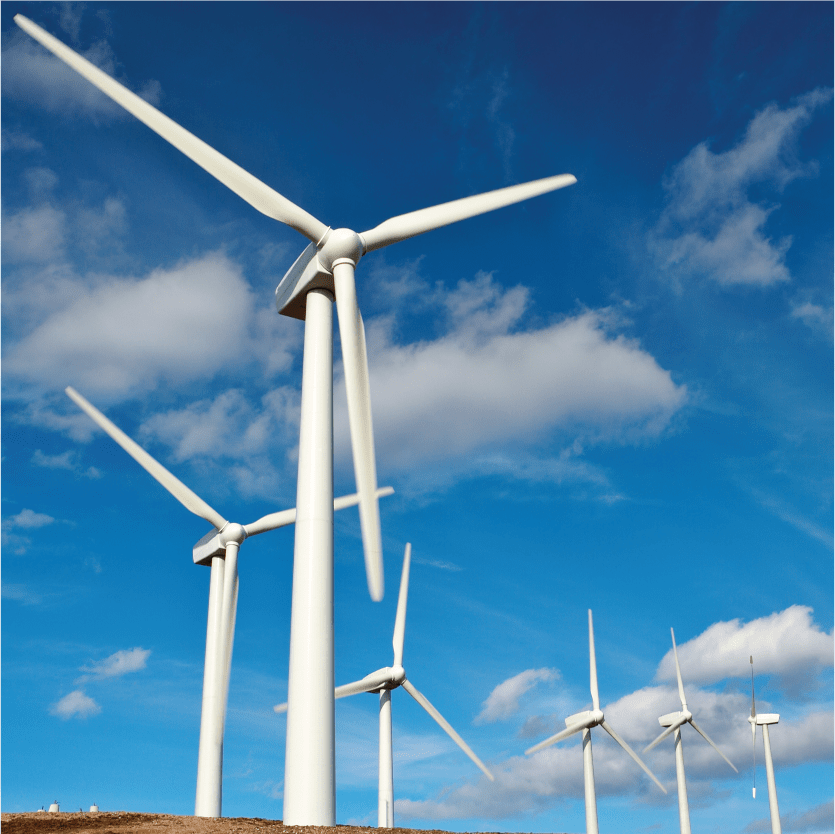
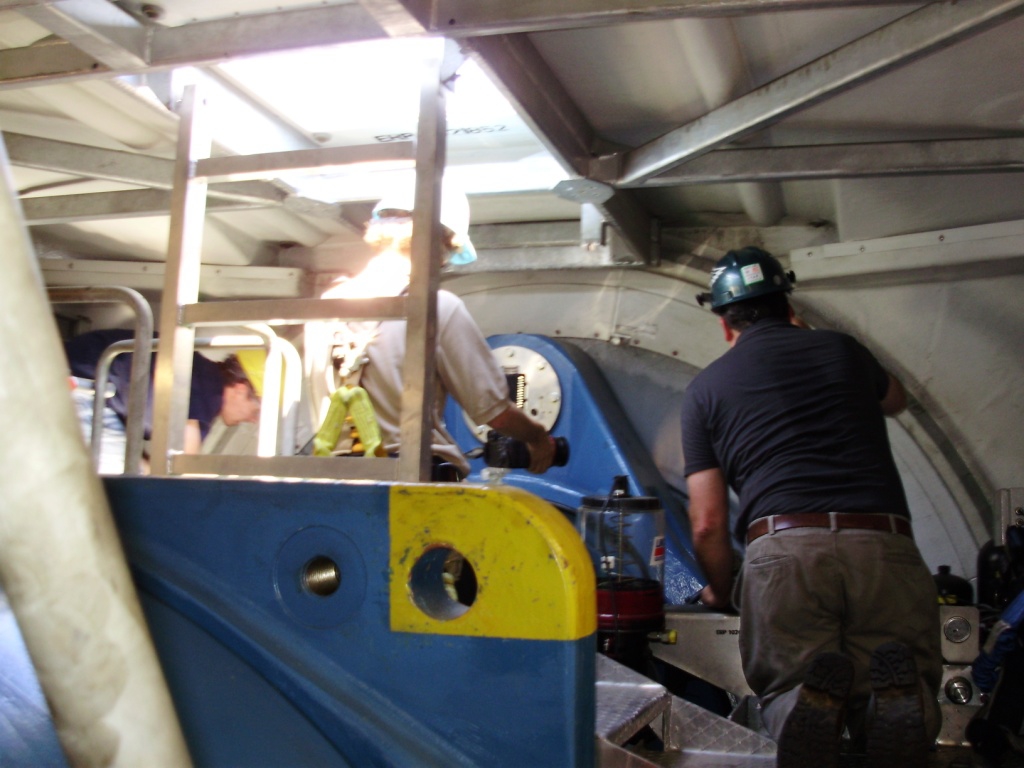